Linear Brushless Motors
Find your linear motor here |
servo motors
unlimited travel
iron core
low cog
LinServ |
 |
Linear
motors
brush-less servo
Iron core
low cog |
Series LC
|
servo motors
unlimited travel
iron core
low cog
dual magnet design
no bearing preload
LinServ
|
 |
Linear
motors
brush-less servo
Iron core
dual magnet track
|
Series
DM
|
|
|
|
|
|
 |
|
Linear Actuators
Find your linear
actuator here
|
direct linear servo drive
integrated bearing
precision feedback
high speed
cabling system
"plug-&-play"
LinServ
|
 |
Linear Actuators
linear servo motor
turn-key solution |
Linear ServoSlideTM
|
direct linear servo drive
integrated bearing
precision feedback
long stroke
"plug-&-play"
LinServ
|
 |
Elevator Stages
linear servo motor
turn-key solution |
Elevator Stage |
direct linear stepper drive
air bearings
LinStep
|

|
Lift
(Z) axis
linear stepper motor
with air bearings
|
Series Z
|
direct linear servo drive
integrated bearing
linear feedback
high cycle rate
"plug-&-play"
LinServ |
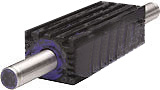 |
Linear
Actuators
linear servo motor
push-pull rod design
|
I-ThrustTM |
motorized screw
integrated bearing
high resolution
"plug-&-play"
|
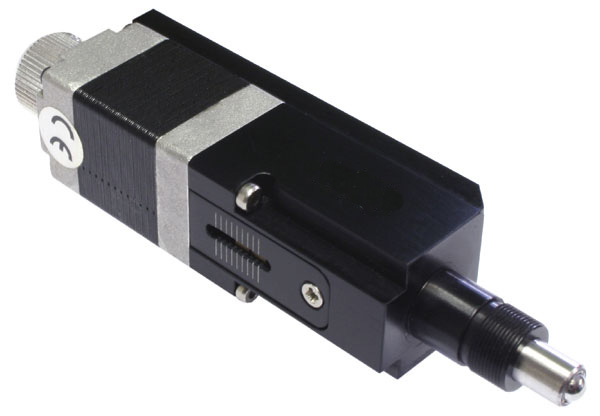 |
Linear
Actuators
Motorized screw
contact factory
|
M-ThrustTM |
direct linear servo drive
integrated bearing
precision feedback
high acceleration
position/force controls
LinServ
|

|
Linear Actuators
linear servo motor
position/force controls
|
I-ForceTM |
direct linear stepper
drive
roller bearings
air bearings
LinStep
|

|
Linear
Actuators
linear stepper motor
with ball and air bearings |
Series BB |
direct linear stepper drive
closed loop operation
Linear ServoStep
|

|
Linear
Actuators
linear stepper motor
position feedback
|
Linear ServoStepTM |
|
|
|
|
|
 |
|
Rotary Tables
Find your rotary table here
|
|
motorized stages
compact design
integrated bearing
center aperture
small size
|
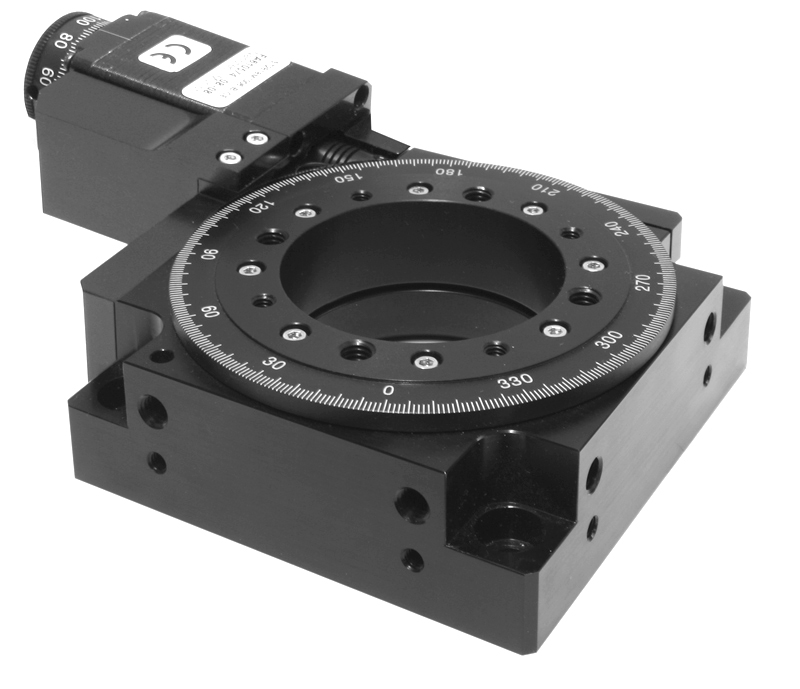 |
Motorized Rotary stages
very compact design
contact
factory
|
Series
RTHM |
motorized stages
compact design
integrated bearing
large center aperture
small size |
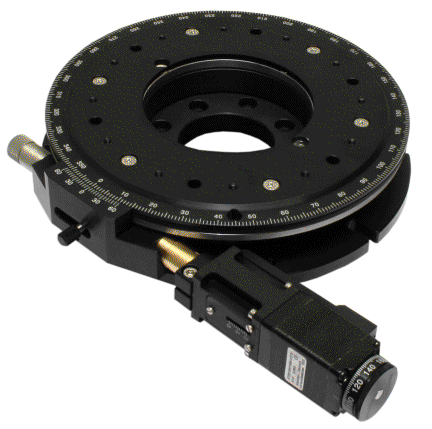 |
Motorized Alignment
Rotary stages
compact design
limited rotation angle
contact factory
|
Series
RTHM-Align
|
direct Z-Theta drive
integrated stage
air bearings
LinStep
|
 |
Z-Theta
system
air bearings
|
Series
ZT |
direct drive
air bearings
very low profile
center aperture
RotoLinear
|
 |
Rotary
Tables
low profile
|
Series RTH |
direct drive
air bearings
low profile
large open center
RotoLinear
|
 |
Rotary Tables
large open center
|
RotoRingTM |
direct drive
integrated bearing
precision feedback
center aperture
medium load capacity
high torque
RotoServ
|
 |
Rotary Tables
medium load capacity
|
ServoRingTM
|
direct drive
integrated bearing
precision feedback
center aperture
heavy load capacity
high torque
RotoServ
|
 |
Rotary Tables
heavy load capacity
|
ServoRingTM
|
direct servo drive
integrated dual bearing
precision feedback
large center aperture
low profile
high speed
|
 |
Rotary Tables
large aperture
high speed |
AccuRingTM
|
direct servo drive
integrated bearing
precision feedback
center aperture
low profile
high speed
RotoServ
|
 |
Planar Rotary Tables
low profile
high speed
|
Planar ServoRingTM
|
|
|
|
|
|
 |
|
|
|
|
|
XY systems
Find your XY table here
|
|
direct drive
single plane XY stage
multiple forcers
air bearings
lightweight construction
large travel area
PlaneStep
|
 |
Planar systems
XY
table
Single plane |
Planar XY |
direct servo drive
robotic
arms
XYZ configurations
linear motors
LinServ
|
 |
XYZ
Robotic Arms
XY table with
Linear Servo Slides
|
Robotic XY
|
direct servo drive
large area travel
XYZ
system
linear motors
LinServ
|
 |
Gantry Systems
XY table
large
area travel
|
Gantry XY |
direct servo drive
XY table with Theta stage
large center aperture
closed loop operation
|
 |
X-Y-Theta workcells
XY table with
open frame |
Open frame XY |
|
|
|
|
|
 |
|
|
|
|
|
Feedback Systems
Find your encoder here |
|
linear feedback
tape-less system
single and XY system |
 |
Linear feedback
for linear stepping motors |
IntelLiCoderTM |
open tape system
sub-micron resolution
feedback for servo motors
built-in interpolation |
 |
Linear encoders
open tape system |
|
enclosed system
small profile
feedback for servo motors
hi-accuracy
built-in interpolation |
 |
Linear encoders
enclosed system |
|
large open center
small profile
hi-accuracy
measures through 360° |
 |
Ring encoders
large open center |
|
1-3 axes
relative/absolute position
linear/rotary compatible
index position capture
PC interface |
 |
Encoder digital readouts
1 to 3 axes |
|
|
|
|
|
|
 |
|
|
|
|
|
Control Electronics |
|
credit card size
hi-res micro-stepping
closed loop ServoStep
40VDC/3Аmp
|
 |
Smart drives and indexers
PCB
|
I-DrivesTM |
panel mount
hi-res micro-stepping
closed loop ServoStep
80VDC/6Аmp
|
 |
Smart drives and indexers
panel mount |
I-DrivesTM |
RS-232 network
stand-alone indexer
hi-res micro-stepping
PLC interface
110/220AC
|
 |
Programmable standalone
Networked
indexers
|
I-StepTM |
CAN network
stand-alone indexer
closed loop servo controls
sinusoidal commutation
PLC interface
110/220AC
|
 |
Brushless servo amplifiers
Networked indexers
|
I-ServTM |
multi-axes controller
(1-8)
closed loop servo controls
micro-stepping controls
Ethernet network
PCI, ISA, VME, PC104
|
 |
Multi-axes motion controllers
|
|
|
|
|
|
|
|
|
|
|
|
 |
|
|
Last update 05/29/2010
Linear actuators, rotary tables
and XY tables for your motion automation task |
|
|
|
|
|
|
Benefits of a Rotary Table
A rotary table is a precision device that is
ideal for work positioning. Such table is used in metal works as it
makes the job of drilling easier for the metal worker. Other than
this, the metal worker can also cut the piece on fixed axes during
specific interval with the help of a rotary table.
Rotary tables
are available in varieties. Some of these tables use
indexing plates for operations related to indexing whereas, others
enables the user to fit dividing tables and leads to a better work
positioning.
What make rotary tables important for metal
industry are its numerous uses. Here is a list of few:
--
Rotary tables are used for machining spanner
flats on bolts
-- For cutting round pieces
--
For drilling holes at equal distance on circular flanges
-- A metal worker can also create large diameter
holes on milling machines with these tables
There are different parts and components in rotary
tables and all have different functions. Work table is the most
important part of the table. It has spherical working area with four
t-slots, which are used for mounting work pieces. There is a clank
handle on rotary tables that enables the user to rotate the
tables in clockwise and anti-clockwise directions.
Rotary tables also have two bases, one is
meant for vertical rotation whereas the other one is meant for
horizontal rotation.
At times, rotary tables are also mounted flat
on planes similar to the way cutters are placed on vertical milling
machines.
If we look closely, rotary tables play a
crucial role in the metal industry. Because they are used to perform
different jobs, there is a specialized variety of rotary table
to meet industry specific needs.
|
Functioning of Rotary Tables
Rotary table is a work positioning device that
has got high usage in metal working as it enables the metal worker
to cut or drill the piece at exact intervals. There are some rotary
tables that also enable the worker to perform indexing operations
while the others can be fitted with dividing plates for work
positioning.
Rotary Tables are mounted flat on the tables that are
rotating around vertical axis in the plane of the vertical milling
machine. There is also an alternate setup where tables are mounted
on the ends of machine for rotating around horizontal axis.
When the table is mounted on a secondary table, the
work piece lies at the center around the axis of the table that is
centered around the axis of the cutting tool. All these three axis
lie in coaxial form. In order to set the cutter at the desired
distance from the center of the work piece, the secondary table is
offset in X or Y direction. This will result the worker to perform
concentric machining operation on the work piece. If you want to cut
more complex curves, it is suggested to place the work piece
eccentrically at a fix distance from the center.
If you are setting the table on vertical mill, you
can either drill concentric or equidistant holes as well as cut
semicircular shapes & contours.
If we list the benefits and uses of rotary tables,
they are used:
·
For machining spanner flats on bolt.
·
For drilling equidistant holes on the circular
flange.
·
For cutting round pieces with protruding tang.
·
For creating large diameter holes on small milling
machines through following a circular toolpath.
·
For milling helixes.
·
For cutting difficult curves.
·
For cutting straight lines.
·
For cutting arcs.
A rotary table has a solid base so that it can
be clamped onto another fixture or table. These tables have an
important usage in the metal work industry because of numerous
functionalities.
|
Buying Tips for Rotary Table
A
rotary table is used in precision metalworking industry. It is made
of a solid base that can be clamped on to the other fixture. In
simple words, rotary tables are discs, which rotate freely or by
using a worm drive with a motor.
Rotary tables are used in different applications like machining,
assembly and automation. Other than this, these tables find usage in
assembly and equipment positioning. When you are buying a table,
there are a few things to consider. These include:
Diameter of the Table
The worktable diameter is the surface area of the rotary table.
Measurement of Through-Hole Diameter
It is the diameter of the breadth of the hole present at the center
of the workstation.
Maximum Radial Load
When the load is pushed against the table, the heaviest amount it
can support on vertical or horizontal axis is the maximum radial
load.
Maximum Axial Load of the Table
Maximum weight tables are able to bear at the time of concentric
operations.
Table Rotation Speed
Maximum rotation speed set b the manufacturer.
Minimum Indexing Increment
Smallest angle setting on the table.
Rotary tables can be mounted in horizontal, inverted or vertical
styles. When the table is mounted horizontally, it is in a flat,
horizontal and upright position. In vertical mounting, surface of
the table runs up and down. When it is inverted, the table is upside
down in a horizontal angle.
The location of drive on rotary table depends on the mount. You can
place the drives below, behind, on the top or on the side of the
table. When the drive is mounted horizontally, it is located above
the surface of the table. When the table is mounted horizontally,
the side-mounted drive is placed to the side of the surface of the
table.
The rotary table can be driven manually, pneumatically,
hydraulically and electrically. If you are driving manually, the
table should be loosened and it must be turned manually with the
crank.
|
|
Components and
Uses of Rotary Tables
|
|
Rotary table
enables the process of drilling holes on a drilling rig by providing
rotational force to the string of the drill. It is a precision work
positioning devices that is used in metalworking. With such a table,
an operator can cut or drill the work around a fixed axis. Here are
the components of a rotary tables:
Rotary Locks
Almost all the
rotary tables have rotary lock. The lock prevents the table from
turning in one direction or from turning at all. This component is
mostly used as an alternative of using a second pair of tongs for
breaking out or making the pipe.
Chain Drive
Most of the rotary
actuators are operated by chain. These chains are similar to the
large bicycle chains and you need to constantly oil them to prevent
from jamming or burning.
Bushings
Bushings are
present at the center of the tables and can be removed in two
separate pieces. The large gap in the rotary bushing center is
called bowl. In bowl, slips are set for holding the drill string
when the pipe and connections trips. These bushings connect to the
Kelly bushings for inducing the spin which is required for drilling.
Most of the
rotary tables are nowadays no coming with rotary drives.
Instead, they have top drive technology where the drill string is
moved by mechanism located at the Kelly.
There are some
rotary drives that use index plates for the purpose of indexing,
whereas, others come with dividing plates. These plates lead to the
regular work positioning at divisions where indexing plates cannot
be used. Rotary actuators are used for machining spanner flats on
bolt, for drilling equidistant holes on circular flanges, cutting
round pieces as well as for creating large diameter-holes which
small milling machines fail to do.
|
Mounting of the
rotary table
|
|
How to mount rotary tables to
maximize performance. Various ways to mount rotary table.
|
|
Rotary indexing
tables have demand in metalwork industry because they are accurate
labor locating tools. An operator can disjoint the piece or pierce
through it within a determined axis with the help of a rotary stage.
There are a few
rotary CNC tables that enable the utilization of index platters for
indexing maneuvers whereas others can be added with dividing plates
for assignment arrangement within junctions.
Mounting of Rotary Tables
These tables are
mounted in a flat manner so that tables are positioned in revolving
way around the perpendicular alignment. This kind of job is done on
the rotary dial table, while keeping a steady plane perpendicular to
milling machine. There is one more optional arrangement for rotary
index tables, where they are mounted at a right angle plate so that
they can be revolved on a parallel axis. You can also use
tail-stocks in this arrangement to securely place rotary tables work
pieces at the center.
In case you are
mounting the table on a resulting table, the workstation will be
centered in the circumference of the alignment. The axis of the
table will fall in the middle of the axis of the cutting apparatus.
In this way, all the three alignments will be coaxial and will share
familiar axis.
Other than
positioning the machine spanner flats on bolt, you can use rotary
tables to make holes on the top of a spherical projection at equal
distances. One of the amazing functions of these tables is making
big diameter punctures with the help of a round tool path.
Rotary Tables when coupled with CNC milling machine work as
stepper motors. These tables accept multiple components that are
included in a mill and also remove the need for lathe machines. It
is because of multiple advantages of rotary tables, they are
important in metal work industry.
|
Direct Drive Rotary
Table Construction
|
|
Torque motors are also
called "frameless" motors. They don't have housings,
bearings, or feedback devices.
In this sense the motor is a kit
and meant to be part of the
machine structure.
Torque motors are designed as
direct drives. They eliminate
the need for gearboxes,
worm-gear drives, and other
mechanical transmission elements
and directly couple the payload
to the drive. This makes
rotary drives with high
dynamic responses and no hysteresis
possible. The large inner
diameter of a torque motor is a
big advantage in machine
tool design. Large
hollow shaft allows designers
to design rotary table to support bearings,
feedback devices and payloads.
Torque motors are available in a
wide range of sizes, with
diameters from smaller than 100
mm to larger than 1 m. Motor
diameter is similar to frame
size for conventional brush-less servomotors. And for a given
diameter, several axial lengths
are available.
Torque motors have a
large number of magnetic
pole-pairs with many permanent magnets on
the rotor. Torque
motors can be built as thin
rings. They
have smooth velocity modulation
with low ripple. Eddy-current losses in
torque motors constrains
the maximum practical number of
pole pairs and speed. As a result, torque
motors are primarily designed
for low/mid-speed range applications,
generally below 1,000 rpm.
Torque motors produce high
torque at stall and can have
high dynamic stiffness. However,
the motor alone does not
determine dynamic stiffness or
precision. To exploit the full
benefits of direct-drive,
an integrated
rotary table must also contain precision
feedback device and high stiffness
bearing to provide a
high-performance rotary stage.
High-precision, high-resolution
feedback is essential for
optimal performance of rotary
tables. Because loads are
directly coupled to the drives,
higher accuracy is possible.
Rotary table
positioning resolution is also
in direct relation to the
feedback's resolution, so it
takes an encoder with a
high line count and a
high resolution interpolation
factor. System resolution below 1 arc-sec
is achievable in direct drive
rotary stages..
An
important difference between
direct-drive rotary tables and those
driven by conventional dc
servomotors and gearboxes is
that torque motors are found
inside the rotary table axis and are part of
the machine. Most of torque motors include
provision for liquid cooling which effectively
increases the continuous torque
rating of the motor and higher
power rating of the rotary
table. Air
cooling, while an option, is
much less effective than
liquid-based cooling.
A
torque motor is only one
element in a complete rotary
stage. It
still needs a mechanical
structure with high rigidity and
precision
bearings. It is
an overall integration of
these elements that determines
complete rotary stage performance. |
|
|
|
|
|
|
|